Technical Innovation
SO3D. has developed a process for manufacturing 3D textile reinforcements
volume with weft insertion. Advantage: to produce structures with very
complex, compact on several thicknesses, without cutting or adding, which
current techniques do not allow.
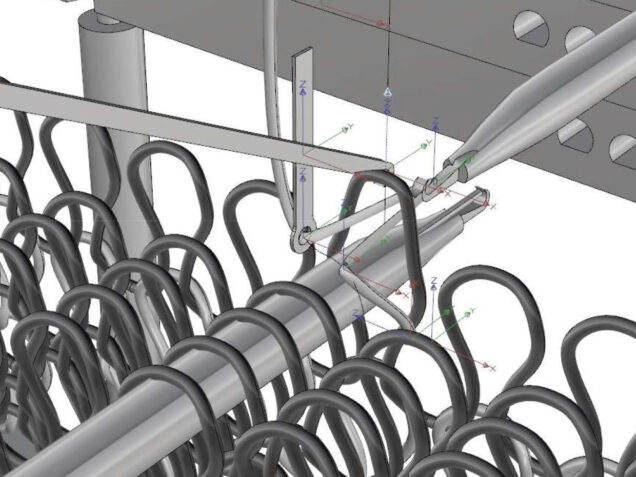
The millennial tradition of weaving and textile manufacturing is revitalized with a new, innovative approach. This new method is based on 3D printing techniques, which use fusible materials to create bonds between fibers. The ancient manufacture of tablecloths and textiles is thus revived, paving the way for a new era of technical textiles.
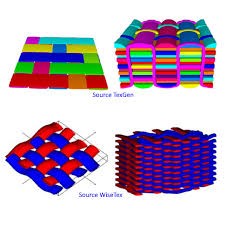
Textile technology is reinventing itself, with a focus on eliminating delamination in structural reinforcements. The classic multi-layer method deposited by robots in terms of bonding. Our real 3D approach makes it possible to weave, knit or braid thick and compact layers, which are then bonded together to overcome or even eliminate the major drawback of the traditional laying process: delamination. Either we create no connection between the layers has an absence of connection.
The disruptive innovation SO3D finds its application in the manufacture of woven, knitted or braided dry tablecloths. Traditional weaving and knitting techniques are given an upgrade with a new approach, although the latter does not allow for draping. The SO3D solution revisits these ancestral techniques to adapt them to the modern era of factory 4.0.
To innovate is to try, to fail, to grope, to try again, to persist and to always believe in it. SO3D technologies, SO3D reinforcements and SO3D innovations are the fruit of this innovation process.
We design and manufacture reinforcements for composites, efficient and innovative. Our fabrics, multiaxials, sandwich reinforcements combine with materials such as glass and aramid.
Delamination, which is the separation of the layers of materials during mechanical stress, is the main drawback of superposed plies used in ballistic protection. Our 3D weaving technology was developed in response to this low delamination resistance of laminated composite structures.
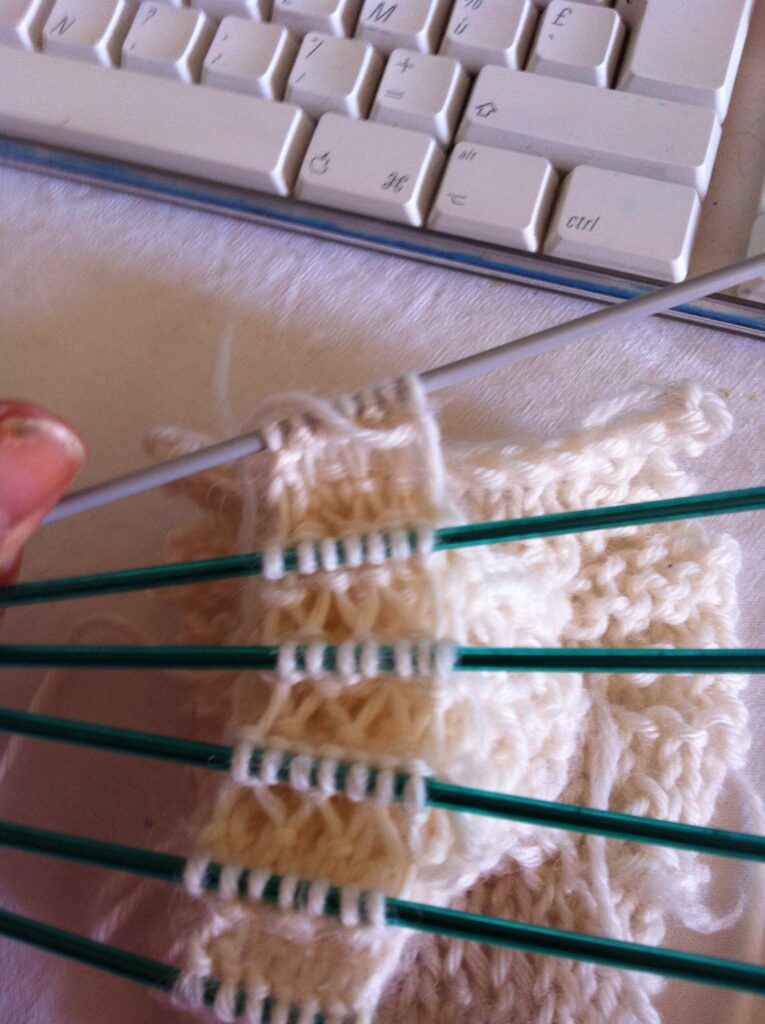
Textile reinforced structural composites are a major discipline of modern research and development. The geometry of the reinforcing fabric plays a crucial role in determining the mechanical performance of fabric-reinforced composites. Unlike conventional materials, structures with textile geometries, or multiaxial fabrics, can be designed and developed to resist in a particular direction.
There are several methods of making fabrics from textile fibers. The most common interlacing is weaving, where two sets of threads intersect and intertwine. Another form of interlacing, called knitting, involves one yarn from one set interlocking in the loops of a neighboring yarn. Our SO3D solution is positioned at the crossroads of these two methods, bringing a new dimension to the textile industry.
Advantages
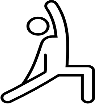
Flexibility

Lightness
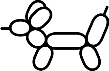
Complex shapes

Single operation
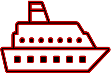


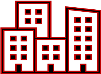
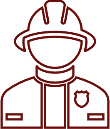